Manufacturing of Socks
Knit into a tube
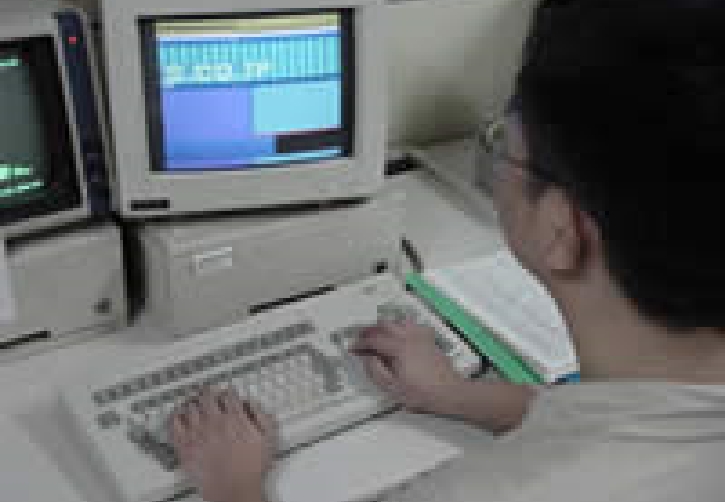
#01
Design data creation
First of all, I make data of sock style (high socks, sneaker socks, etc.) and color scheme design.
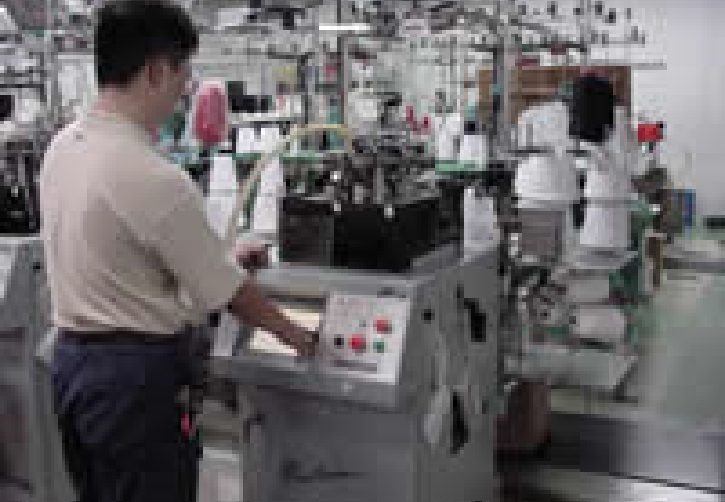
#02
Determination of material
Decide the material to use (cotton, wool, acrylic, etc.) and knit with a machine.
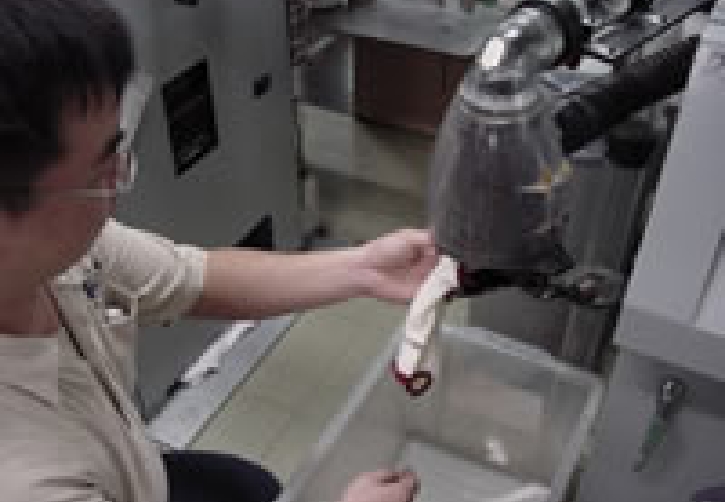
#03
Knitting
One leg is braided in about 4 minutes and comes out of the machine.
Inspection of fabric surface
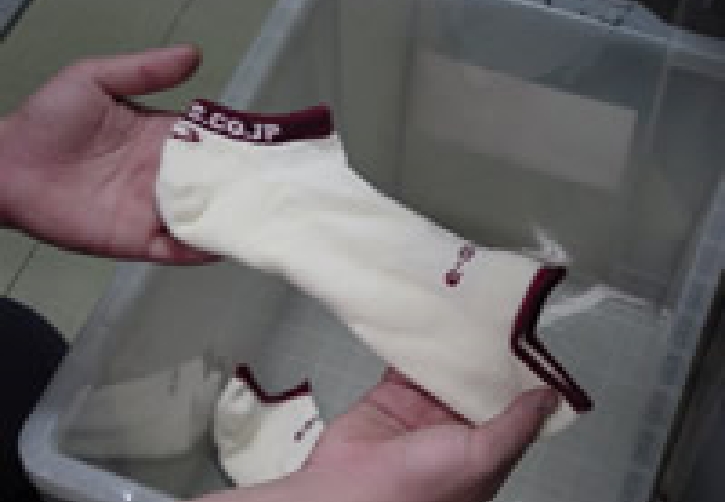
#01
Open toe
It is not ready to be worn, the toe is open (tubular).
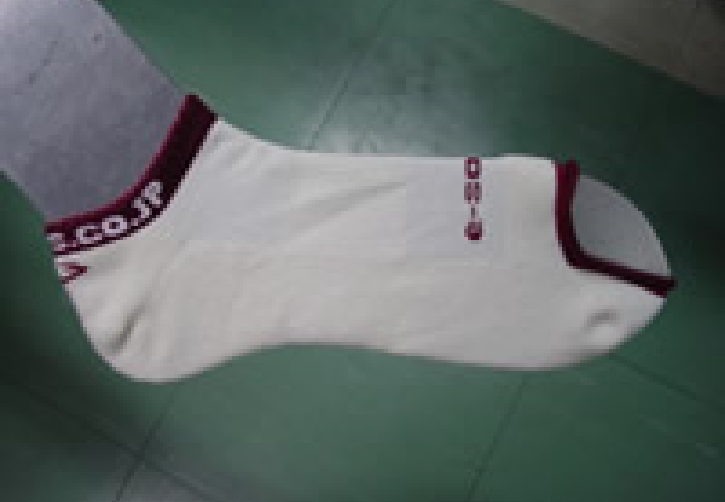
#02
Surface inspection
Place it on the inspection board and check the surface for scratches, dirt, etc.
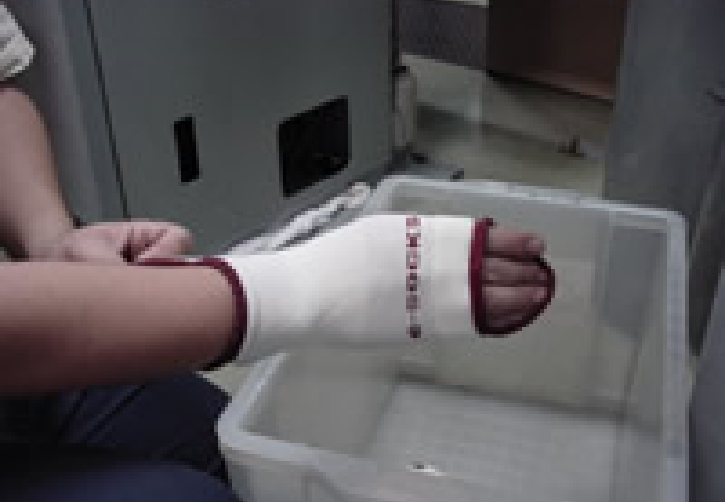
#03
Confirmation of feel
Check the texture of the fabric by hand.
Sew up the toes to form a bag
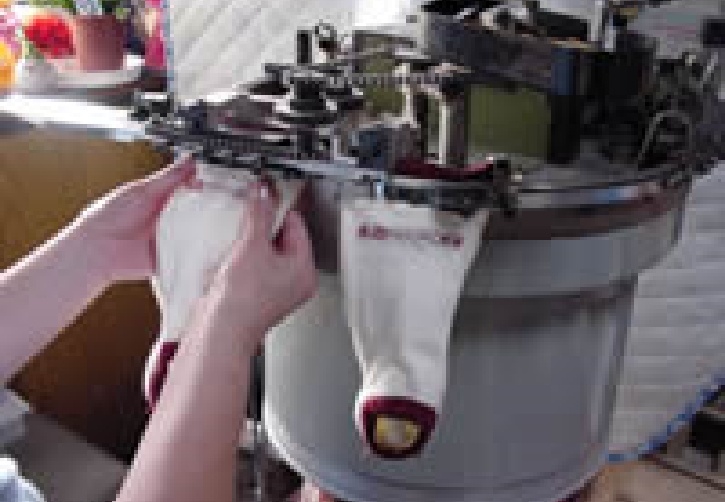
#01
Suture toes
Sew the back side one by one with a special sewing machine so that the seam does not appear on the front side.
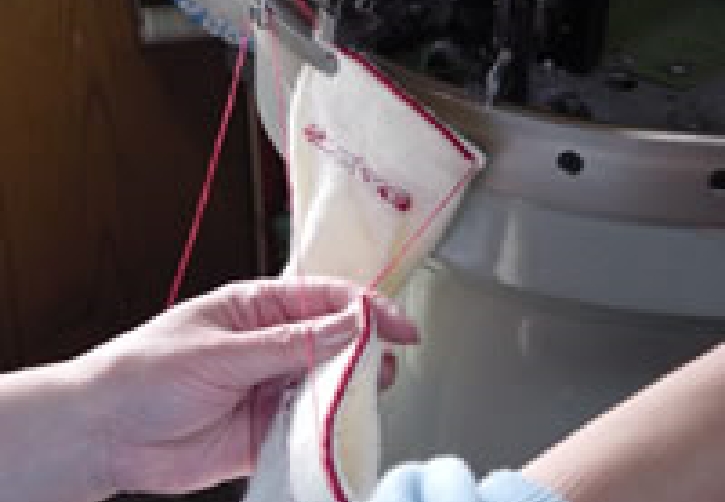
#02
Fully automatic suturing process
It will be sewn in about 1 minute fully automatically.
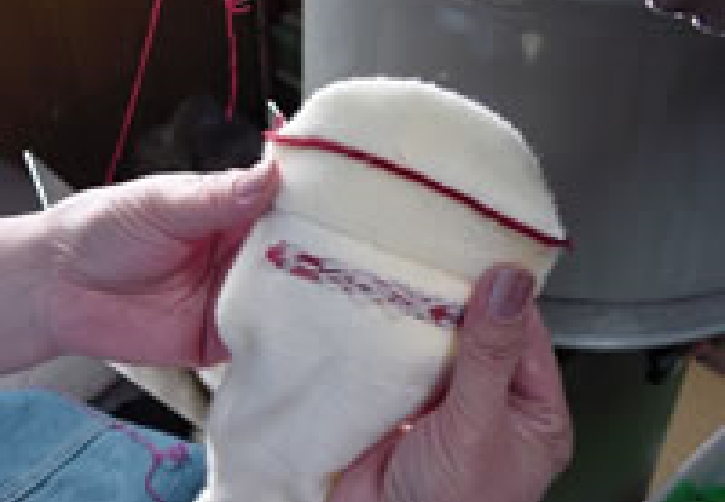
#03
Toe suturing completed
The tubular toe has been sewn.
Prepare the surface of the dough
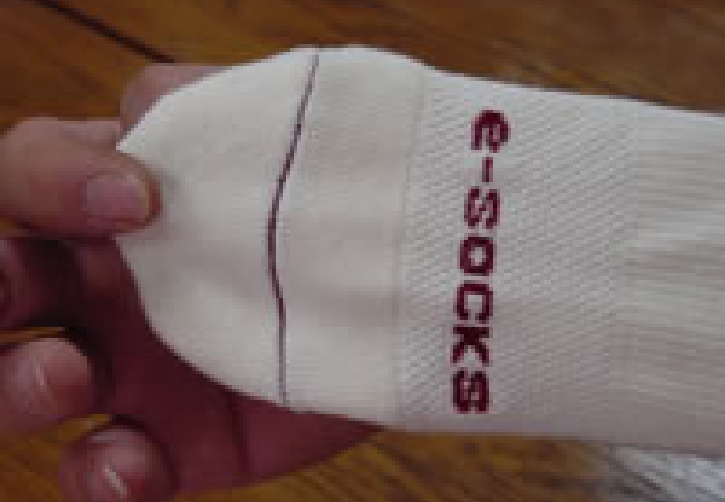
#01
In a bag-like “sock”
The toes are closed and almost sock-shaped.
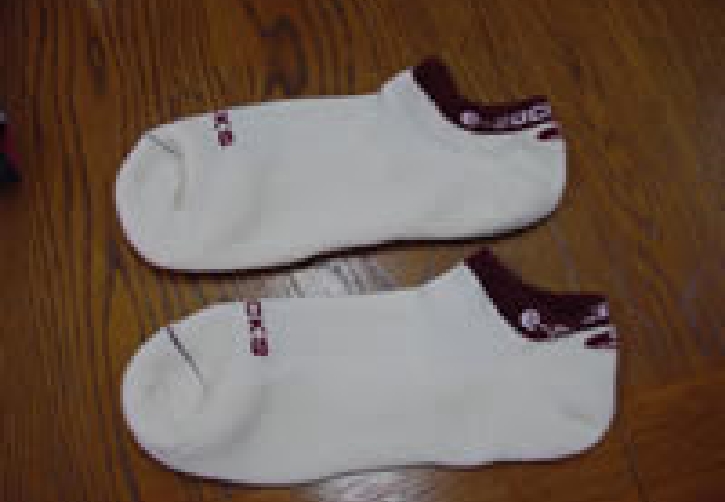
#02
Check for fabric wrinkles
The shape of the sock has been changed, but there are wrinkles on the fabric surface.
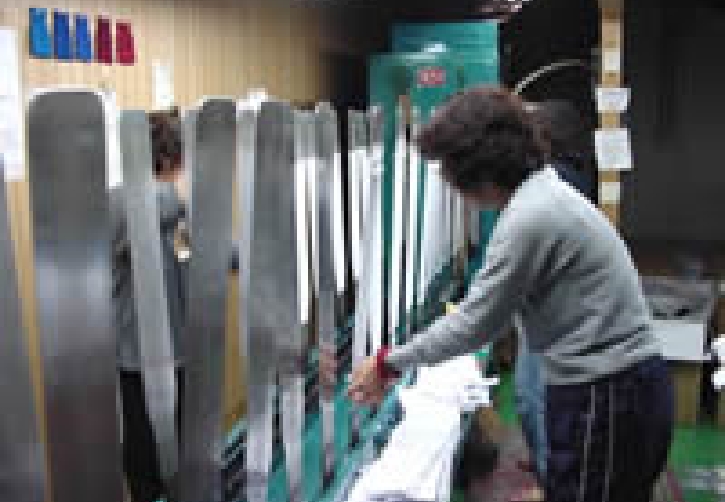
#03
Set socks on machine
Next is the work of setting up the dough. Fit socks into the flowing metal plate one by one.
Packaging
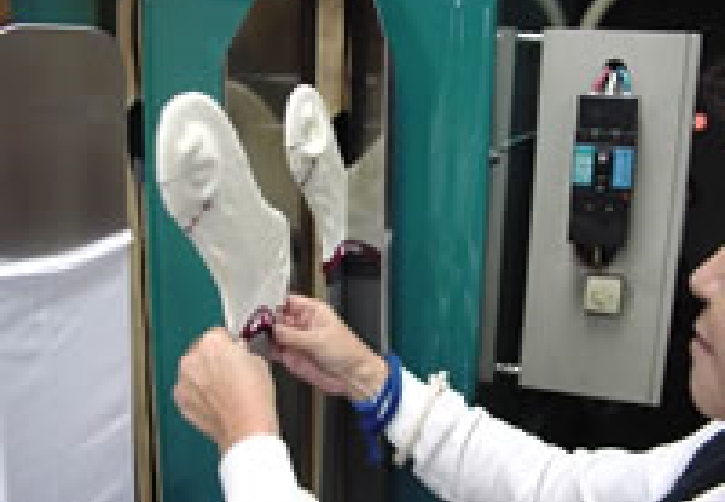
#01
Removes wrinkles from dough with heat
This back is quite high temperature (170 ° C), and wrinkles etc. are eliminated by the feeling of ironing by heat, and the fabric surface is adjusted.
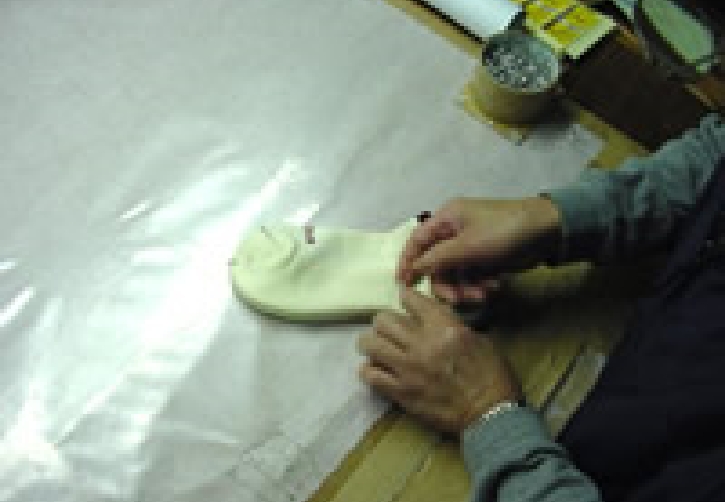
#02
Label and packaging
Finally, the packaging work. Attach a size sticker or various label stickers and put them in a bag.
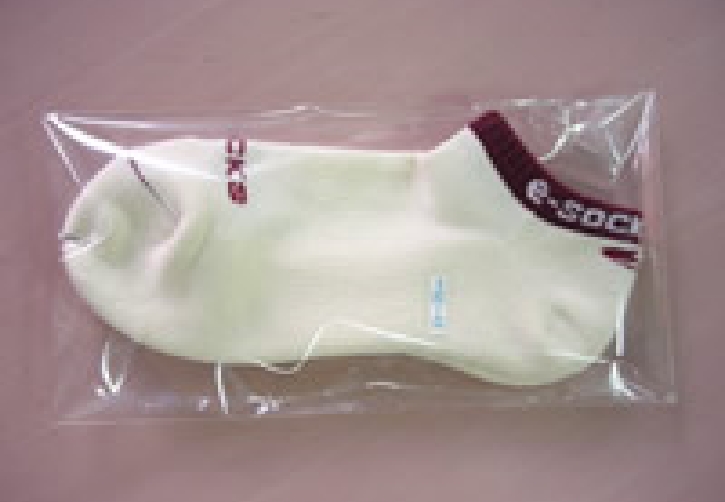
#03
Package completion, shipping
After all processes, socks are completed.
Founding Place
Japan’s best shoe manufacturing
Koryo-cho, Nara Prefecture, is Japan’s largest sock production area
Koryo-cho is called “Yamatokoku Hirosegun”, where “Yamato cotton” has been used as a raw material for socks for a long time. Tajiro Yoshii started “manufacturing socks”.
I bought a sock knitting machine from the United States, and in 1910 (Meiji 13) gathered the daughters of neighboring farmers and started making socks. In 1951, the domestic production of nylon material triggered a dramatic increase in production.
Nylon socks, which can be stretched and stretched and have excellent fit, have fueled the economy of the region, and Koryo has finally become the largest sock producer in Japan.